In accordance with the European Union’s General Data Protection Regulation (GDPR), we are committed to safeguarding and ensuring your control over your personal data. By clicking “Accept All” you are permitting us to use cookies to enhance your browsing experience, assist us in analyzing website performance and usage, and deliver relevant marketing content. You can manage your cookie settings below. By clicking “Confirm” you are agreeing to the current settings.
Vapor Chamber Heat Sink: Unlocking Superior Cooling
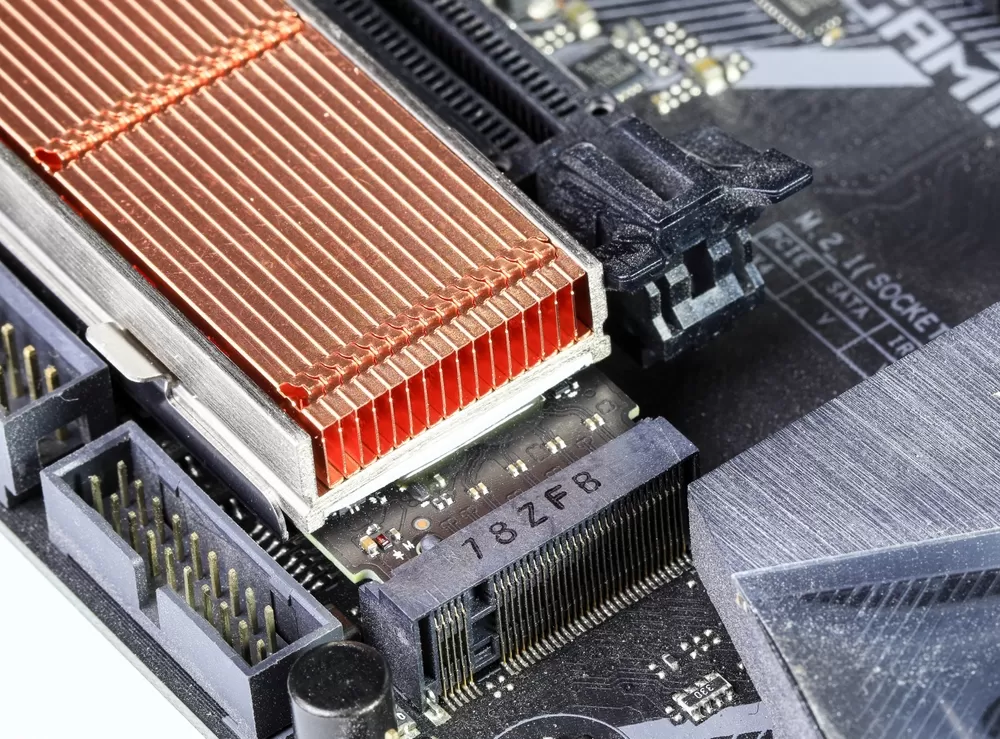
Vapor chamber heat sinks are key for high-power electronics thermal management due to their reliability. Traditional heat pipes struggle to manage hotspots and consistent temperature distribution when devices shrink and power densities rise. To satisfy these criteria, ultra-high thermal conductivity and two-dimensional heat dispersion in vapor chambers decrease thermal resistance. Therefore, such thermal solutions are being used due to the increased requirement for effective cooling in high-power CPUs, GPUs, and other components.
What are Vapor Chamber Heat Sinks?
Vapor chamber heat sinks are thermal management devices that dissipate high-power electronics heat. A flat, enclosed copper chamber holds a small deionized water. The liquid is evenly distributed for optimum heat transfer with a sintered copper wick construction. Unlike traditional heat sinks, vapor chamber heat sinks use two-phase cooling, and the liquid evaporates at low pressure. Remember, the heat sink with a vapor chamber and heat pipe spreader (no-cut fins) might have 50-55% lower thermal resistance than the flat plate casing.
Plus, they lower the thermal resistance of aluminum heat sinks by 30% and copper heat sinks by 20%. Vapor chamber heat sinks can avoid hot spots on parts using thermal design powers from 100-1000 Watts with an even temperature distribution. Such heat sinks may enhance thermal performance by 3-10°C in confined situations where heat sources must be spread out.
The Composition and Design of Vapor Chamber Heat Sinks
Materials Used in Vapor Chamber Heat Sinks
The enclosure and wick of vapor chamber heat sinks tend to be copper. Pure copper is essential for effective heat transfer thanks to its high thermal conductivity of around 400 W/m•K. The chamber normally consists of two copper plates. Also, sintered copper powder balances capillary action and vapor space within the wick structure. Note that in some instances, chambers may have a maximum thermal conductivity of about 20,000 W/m•K.
Aluminum fins can save weight, but thermal performance suffers. Deionized water acts as the working fluid because its latent heat of vaporization improves the vaporization-condensation cycle. The chamber's vacuum-sealed atmosphere lowers the water's boiling point. It allows quick phase transition at low temperatures and boosts thermal management.
Design Variations
The traditional two-piece vapor chamber heat sink has two stamped copper plates. After installing the wick and internal supports, these plates diffusion-bond. The structure is strong and can withstand power densities up to 50 W/cm². High versatility in wick design allows various thicknesses, porosity, and grooved arrangements. For instance, vapor chambers may have aspect ratios of 60:1 or more, unlike heat pipes, which have a 4:1 ratio.
Hybrid one-piece vapor chambers start with a copper tube flattened and machined into a planar shape. High-volume production may save on tooling. One-piece designs enable post-production bending (L-shaped combinations) that two-piece designs cannot. They might decrease thermal resistance over multi-heat pipe alternatives despite being easy to make.
The Advantages of Vapor Chamber Heat Sinks
-
Extremely high thermal conductivity.
-
Efficient heat spreading over a large area.
-
Better performance than copper and aluminum heat sinks.
-
10-30% lower in thermal resistance than heat pipes.
-
Uniform temperature distribution across the heat sink.
-
Effectively manage high heat flux and power density.
-
Thin and lightweight design.
-
Suitable for compact and space-constrained applications.
-
Better isothermalization at the chip interface.
-
Lower overall heat sink delta-T.
-
Better cooling for high-performance CPUs, GPUs, LEDs, etc.
-
Decreased fan noise due to lower operating temperatures.
-
Customizable for particular applications.
-
Prolonged existence while preventing overheating.
-
Flexibility in design and material selection.
-
Cost-effectiveness in mass production scenarios.
-
Dependable performance in harsh environments.
Applications of Vapor Chamber Heat Sinks
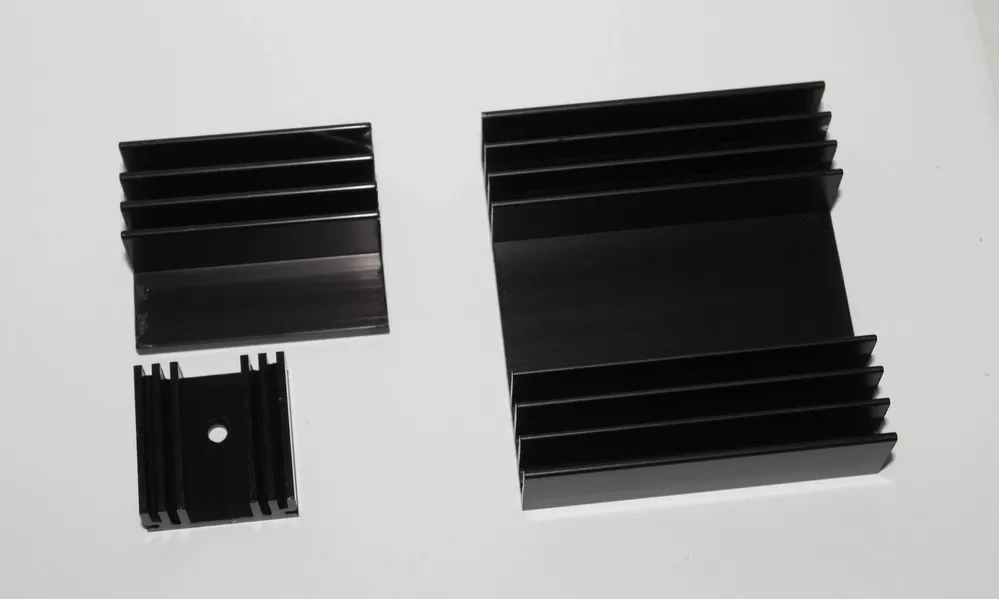
- Thermal Management in Server CPUs: High-density server CPUs create heat. Vapor chamber heat sinks avoid hotspots by spreading heat. Airflow is limited in blade servers, so vapor chambers uniformly distribute heat to decrease thermal throttling better than heat pipes.
- Power Electronics Cooling: Power electronics, including MOSFETs and IGBTs, operate under high thermal loads. Vapor chamber heat sinks spread superior heat and reduce thermal resistance. They are key to compact power supplies with limited space.
- GPU Performance in Data Centers: In GPU-intensive AI and deep learning, vapor chamber heat sinks are important. They spread the heat across the GPU surface. It preserves performance and expands the life of the GPUs under constant heavy workloads.
- Thermal Management in High-Power LEDs: High-power LEDs generate intense heat in small areas. Vapor chamber heat sinks are key to LED cooling in large display panels. They prevent thermal degradation for stable brightness and durability of the LEDs.
- Cooling Solutions in Telecommunications Equipment: Telecommunications base stations demand reliable cooling under punitive conditions. Vapor chamber heat sinks help manage heat in RF amplifiers. Keeping low temperatures impacts signal and system uprightness.
- Application in Aerospace Electronics: In aerospace applications, weight, and thermal management are critical, and vapor chamber heat sinks are lightweight and efficient. They cool avionics and other high-power electronics for stable operation in punishing conditions.
- Multi-Device Cooling: Vapor chamber heat sinks cool multiple parts concurrently. They suit compact electronics, where multiple heat sources need heat dissipation. In server motherboards, a single vapor chamber manages the heat from many high-power processors.
Vapor Chamber vs Traditional Heat Sinks
At high heat flux, vapor chamber heat sinks beat typical heat sinks in thermal efficiency. In certain cases, a vapor chamber can handle heat loads up to 500 W/cm². It is unlike standard heat sinks that rely on conduction and less effective heat spreading. Vapor chamber heat sinks lower thermal resistance, which helps high-performance electronics maintain low junction temperatures. The lower thermal resistance and better heat dissipation are because the working fluid absorbs heat and evaporates, moving heat throughout the chamber.
Vapor chamber heat sinks are essential in high-power HPC, data center, and GPU applications. For example, where a traditional heat sink would raise the temperature to 60°C above ambient, a vapor chamber could limit this to under 30°C. Vapor chambers' small size and good heat distribution make them ideal for minuscule designs like mobile electronics.
T-Global | Innovative Vapor Chamber Heat Sink Solutions
T-Global vapor chamber heat sinks provide expert thermal management, homogeneous heat distribution, and efficiency in small designs. They may be customized for applications with unique shapes, material choices, and integration options for performance. Our engineers work with clients to improve thermal solutions for electronics and automotive systems. Click here to learn more about our vapor chamber heat sinks for exact thermal control for your projects.