In accordance with the European Union’s General Data Protection Regulation (GDPR), we are committed to safeguarding and ensuring your control over your personal data. By clicking “Accept All” you are permitting us to use cookies to enhance your browsing experience, assist us in analyzing website performance and usage, and deliver relevant marketing content. You can manage your cookie settings below. By clicking “Confirm” you are agreeing to the current settings.
Exploring Heat Sink Types: Active vs Passive Heat Sinks
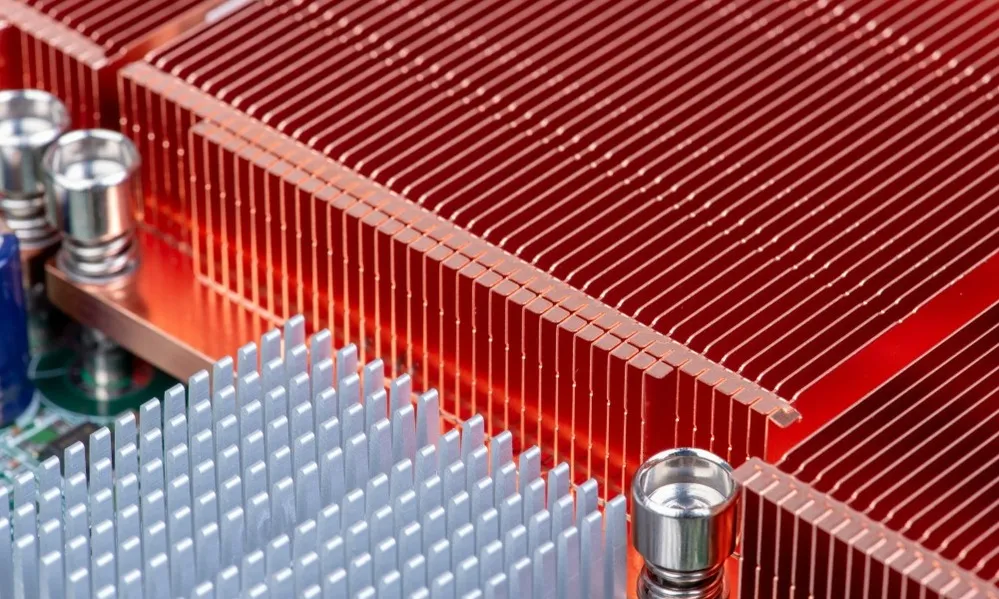
Effective heat management in electronics avoids thermal overload. In this context, active and passive heat sinks are essential. Active heat sinks utilize components like fans or liquid cooling systems to dissipate heat. It offers efficient cooling for high-power applications. Conversely, passive heat sinks count on natural heat dissipation methods like conduction and radiation for environments requiring noise reduction or reliability. Thus, picking the appropriate type of heat sink boosts thermal performance in electronic applications.
Understanding Heat Sinks
A heat sink in electronics dissipates heat from other electronic components. Essentially, it functions as a thermal conductor, transferring heat from electronic devices, including computer CPUs, to a cooler medium like air or a liquid coolant. It is expedited by the heat sink's increased surface area and using materials with high thermal conductivity.
-
General Function
The function of a heat sink is to manage the heat from electronic parts. While dispersing this heat, the heat sink maintains a temperature for electronic devices. The process may involve the passive conduction of heat away from the source, its distribution across the heat sink, and its dissipation into the surrounding environment through thermal diffusion and convection.
-
Importance in Device Longevity
Heat sinks, including passive heat sinks, prolong the life of electronic devices. Overheating is a cause of malfunction or damage in electronics. Heat sinks confirm that components like processors, power supplies, and motors operate within safe temperatures for better performance and barred heat-related failures. In high-power electronics or densely packed circuitry, heat generation can be intensive, and the role of a heat sink becomes more critical.
Active Heat Sinks
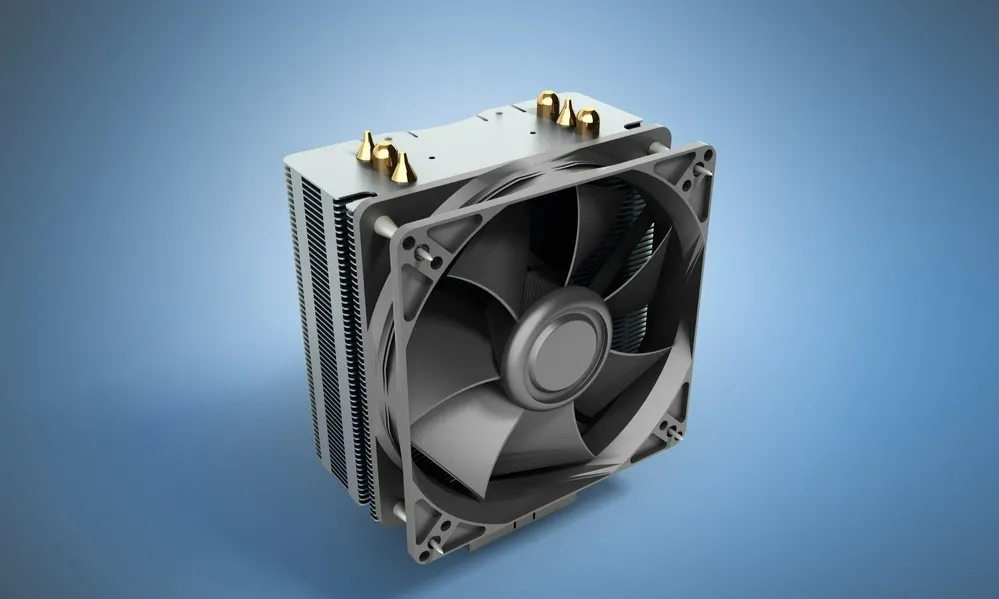
Active heat sinks are cooling solutions in high-performance electronic systems for efficient heat dissipation. Unlike passive heat sinks, active heat sinks incorporate fans or blowers to disperse heat actively. This active airflow augments the cooling efficiency of densely packed electronic components or high-power devices. While moving air over the heat sink, these components assist a quicker and more effective heat transfer away from CPUs or GPUs.
Furthermore, active heat sinks offer the advantage of a more compact design. It is fundamental in current electronics with limited space. They enable more compact and powerful electronic devices with managed heat in a smaller footprint. Their application spans high-performance domains, including gaming PCs, servers, and aerospace electronics.
-
Materials and Design in Active Heat Sinks
Regarding materials, copper and aluminum dominate the active heat sink market. Copper has high thermal conductivity for rapidly absorbing and dispersing heat. However, it's relatively heavy, which can be a drawback when weight is a concern. On the other hand, aluminum offers a lightweight alternative. Though it has lower thermal conductivity, it's effective for heat dissipation. It is used in consumer electronics with weight and cost considerations.
The design of active heat sinks is critical in their performance. The size of the fan, its placement, and the direction of airflow can maximize cooling efficiency. For instance, more giant fans can move more air for better cooling. Still, they take up more space and can be noisier. The placement of these fans can also affect the cooling performance by drawing air away from the heat sink or pushing cool air toward it. Plus, thermal interface materials like thermal pastes or pads develop the heat transfer between the heat sink and the component. They fill microscopic imperfections on surfaces for better contact and heat conduction.
Passive Heat Sinks
In the thermal management systems of electronics, passive heat sinks dissipate heat without mechanical devices. Instead, they rely on natural airflow and thermal conduction. The mechanism transfers heat from a hot component (like a CPU) to the heat sink, dispersing it into the surrounding air. The process is aided by the large surface area of the heat sink, improved by fins or ridges. Their application is expected in less power-intensive electronics with moderate heat load, including LED lighting systems or low-power computer processors.
Likewise, passive heat sinks are reliable because they lack moving parts that can fail. This feature and their silent operation render them desirable in audio equipment. Energy efficiency is another hallmark. They consume no additional power beyond what is needed to run the cooling device. It is helpful in battery-powered or energy-sensitive applications.
-
Materials and Structure in Passive Heat Sinks
Material selection is vital for passive heat sinks. Aluminum is used for general uses thanks to its cost-effectiveness and thermal conductivity. Yet, for higher thermal loads, copper is preferred because of its better heat dissipation properties. The structural design of passive heat sinks, including the arrangement and shape of fins, is noteworthy in their performance. These designs capitalize on surface area for better heat transfer to the ambient air.
Finally, ambient temperature influences passive heat sinks' efficiency. It decreases in environments with high ambient temperatures since the smaller temperature gradient between the heat sink and the air cuts the heat transfer rate. This curb necessitates consideration of the operating environment in the design and selection of passive heat sinks for performance across conditions. For instance, a heat sink with a more aggressive fin design or a combination with other cooling methods might be required in high-temperature settings.
Comparing Active and Passive Heat Sinks
Factor |
Active Heat Sinks |
Passive Heat Sinks |
Cooling Capacity |
Generally higher due to forced air or liquid cooling mechanisms. Can handle more heat from high-performance components. |
Lower than active heat sinks since they rely on natural airflow and heat dissipation. Suitable for low to moderate heat-generating components. |
Efficiency |
More efficient in heat transfer due to fans, blowers, or liquid cooling systems that increase airflow and heat removal. |
Less efficient in rapid heat transfer. Efficiency depends on natural convection and radiation, which can be slower and less predictable. |
Cost |
Initially more expensive due to mechanical components. Also, operational costs can be higher due to power consumption. |
Generally cheaper because they do not require additional components. Have lower operational costs since they don't consume extra power. |
Space |
May require more space for fans, heat pipes, or liquid cooling components. |
Compact and simpler in design, requiring less space. Ideal for applications with space constraints. |
Maintenance |
Requires more maintenance. Fans may accumulate dust and need cleaning. Liquid cooling systems need monitoring for leaks. |
Negligible maintenance because there are no moving parts. Dust accumulation is less of a concern. |
Lifespan |
Shorter life owing to wear and tear of mechanical parts. The risk of failure can affect longevity. |
Longer life since there are no parts that wear out. More reliable over a period, thanks to simpler construction. |
T-Global Provides Heat Sink Solutions
Heat sinks in thermal management are of active and passive types. Active heat sinks incorporate moving parts for boosted cooling. Passive heat sinks depend on natural heat dissipation without mechanical components. The trends in heat sink technology are leaning towards miniaturization and efficiency enrichment; future developments focus on more compact and practical designs. Meanwhile, T-Global offers heat sink solutions, including ceramic heat sinks and non-silicone putty. They stress early engagement in product design for the best thermal management. T-Global also encourages custom inquiries for expert consultations and bespoke heat sink designs. Visit our website for more information.