In accordance with the European Union’s General Data Protection Regulation (GDPR), we are committed to safeguarding and ensuring your control over your personal data. By clicking “Accept All” you are permitting us to use cookies to enhance your browsing experience, assist us in analyzing website performance and usage, and deliver relevant marketing content. You can manage your cookie settings below. By clicking “Confirm” you are agreeing to the current settings.
Oscillating Heat Pipes: Revolutionizing Thermal Management
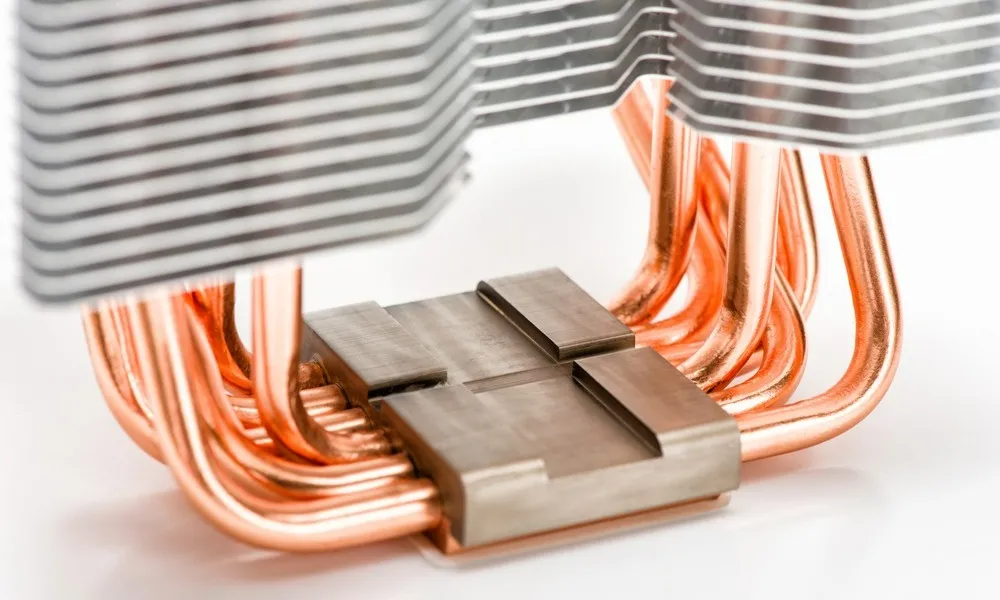
Electronics need excellent thermal management to maintain dependability and lifetime, especially since components create more heat. Meanwhile, oscillating heat pipes (OHPs) are a revolutionary solution thanks to their dynamic phase-change mechanism. Unlike conventional ones, OHPs generate pulsating fluid motion in serpentine channels via rapid vaporization and condensation. OHPs are adaptable because their unique technique overcomes orientation limits and improves heat dissipation in high-heat-flux circumstances.
Understanding Oscillating Heat Pipes
Advanced thermal management systems, including oscillating heat pipes, have a serpentine construction with a working fluid in liquid and vapor phases. This design efficiently transports heat via phase shift and fluid oscillation. The fundamental design speeds fluid vaporization and condensation with several curves and bends. Essentially, this arrangement generates alternating vapor and liquid portions for heat transfer oscillations.
OHPs depend on fluid oscillation. After absorbing heat at the hot end (evaporator), the fluid vaporizes, producing pressure that pushes it toward the cooler end. Heat is released as vapor condenses. Subsequently, pressure differences and pipe oscillation help the condensed fluid return to the hot end. This continuous cycle transfers thermal energy efficiently.
Oscillating heat pipes thrive in thermal management, like massive heat fluxes and fast thermal response. They are helpful for electronic cooling since they can function in any direction and tolerate different thermal loads. Moreover, they assist with keeping optimum operating temperatures in tightly packed, high-power laptop CPUs. Beyond electronics, OHPs are also used in aircraft, automotive, and industrial temperature management.
Working Principle of Oscillating Heat Pipes
As mentioned, oscillating heat pipes use a serpentine tube filled with a working fluid in separate liquid and vapor phases to transfer heat. Heat input at one section evaporates liquid in these pipes, causing vapor that migrates throughout the channel. In cooler regions where heat is extracted, this vapor condenses into liquid. This phase transition causes the pipe's fluid to oscillate, transferring heat from hot to cold locations. Because they can function against gravity, OHPs are adaptable for numerous orientations and applications.
Phase Change Mechanism and Oscillatory Flow of Liquid and Vapor
Oscillating heat pipes have a dynamic evaporation-condensation interaction in the phase change mechanism and oscillatory flow. Fluid droplets in the pipe absorb energy and evaporate into vapor when heated, causing a pressure differential that pushes the vapor toward cooler locations. Latent heat is released when vapor condenses at lower temperatures.
Continually oscillating liquid and vapor along the pipe creates an efficient heat transfer mechanism. This process depends on the fluid's thermophysical characteristics, surface tension, and pipe geometry, which affect heat transfer and oscillatory flow stability. OHPs have excellent thermal conductivities owing to efficient phase transition and flow dynamics for high-performance cooling applications in electronics, aerospace, and automotive.
Design and Structure of Oscillating Heat Pipes
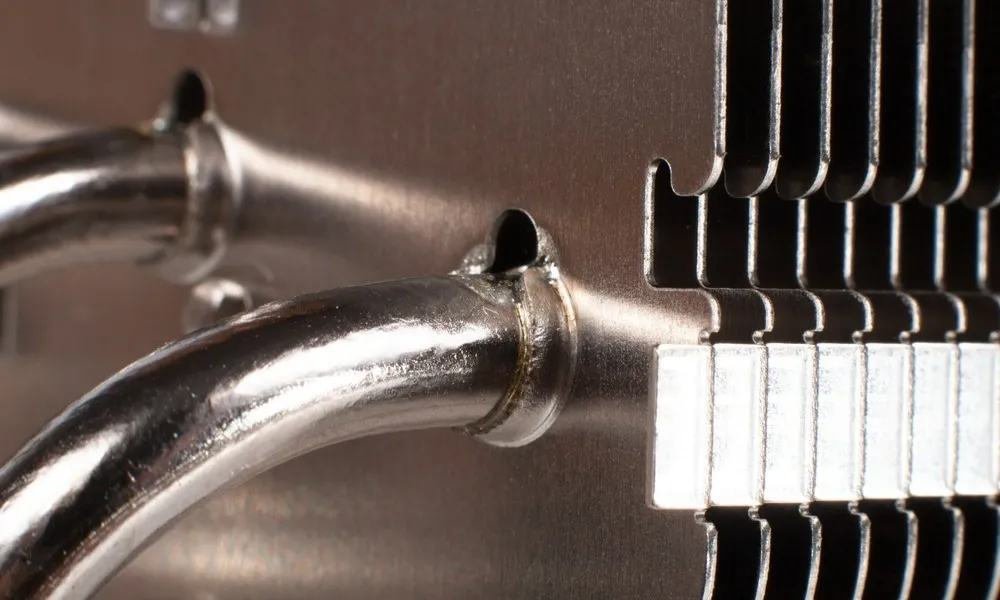
The serpentine channel design of oscillating heat pipes improves thermal management. Unlike linear or straightforward geometries, serpentine pipes bend and curve. The OHP's heat transmission mechanism relies on these bends to keep the pipe's vapor and liquid phases pulsating. This design optimizes working fluid mixing and turbulence for augmented heat transmission. Despite their long pipework, OHPs provide a compact form factor due to their serpentine nature, which becomes appropriate for space-constrained applications.
Contrast with Traditional Heat Pipe Designs
Traditional heat pipes are linear or simple. The working fluid circulates by capillary action, aided by a wick structure on the inside walls. It provides steady, unidirectional heat transmission but restricts heat pipe orientation and flexibility. Oscillating heat pipes respond faster to transient thermal loads than traditional heat pipes. Capillary action and linear construction may limit their usefulness in applications requiring high heat flux control, quick temperature response, or operating against gravity, where serpentine OHPs flourish.
Performance and Stability Limits of Oscillating Heat Pipes
The interaction of two-phase heat transfer and surface tension effects under varied temperature and power settings causes oscillating heat pipes to behave non-linearly. OHPs may be unstable at low power levels owing to inadequate heat input for boiling and vapor production, causing erratic fluid motion. E.g., at lower power, thermal conductivity may oscillate between ~250 W/m•K and ~1000 W/m•K. Vapor formation stabilizes fluid oscillation at greater power inputs for assured heat transmission. So, OHPs are sensitive to heat input, and their operating efficiency counts on the balance between liquid and vapor phases.
Factors Influencing the Stable Operating Range of OHPs
Several factors impact oscillating heat pipes' performance for the stable operating range.
- Gravity may help or inhibit condensate return flow in vertical pipes.
- Another vital aspect is vapor inertia, which overcomes liquid surface tension. Too little may cause fluid motion to fail, while too much can disturb steady oscillation.
- The heat flux, sonic flow limitations, viscosity, and wetting angle also matter. For example, high-viscosity fluids may hinder efficient flow, whereas appropriate wetting angles improve heat transmission via better surface contact.
- Device-specific characteristics like fluid fill-fraction, evaporator, and condenser section lengths determine the operating envelope and manageable heat loads.
Enhancing Thermal Management in High-Heat Electronics
Oscillating heat pipes facilitate thermal management, particularly in high-heat applications like electronics. The serpentine channel in these pipes improves heat transmission via phase shifts and fluid oscillation. Their design lets them work in many orientations, rendering them versatile. Gravity, vapor inertia, heat flow, and viscosity affect OHP performance.
In the interim, modern thermal management technologies set T-Global apart. Our company provides heat sinks, vapor chambers, thermoelectric cooling chips, thermal pads, greases, and putties. These devices are for information, telecommunications, consumer electronics, lighting, medical electronics, and energy. Our expertise and partnerships with key technological R&D centers allow us to provide high-quality, customized thermal solutions.
Our products and facilities are ISO 9001 and ISO 14001 certified for dependability and environmental compliance. Contact us for queries and unique solutions about the oscillating heat pipe technology and thermal management systems.