In accordance with the European Union’s General Data Protection Regulation (GDPR), we are committed to safeguarding and ensuring your control over your personal data. By clicking “Accept All” you are permitting us to use cookies to enhance your browsing experience, assist us in analyzing website performance and usage, and deliver relevant marketing content. You can manage your cookie settings below. By clicking “Confirm” you are agreeing to the current settings.
How Does a Liquid Cooling System Work? What Are the Components?
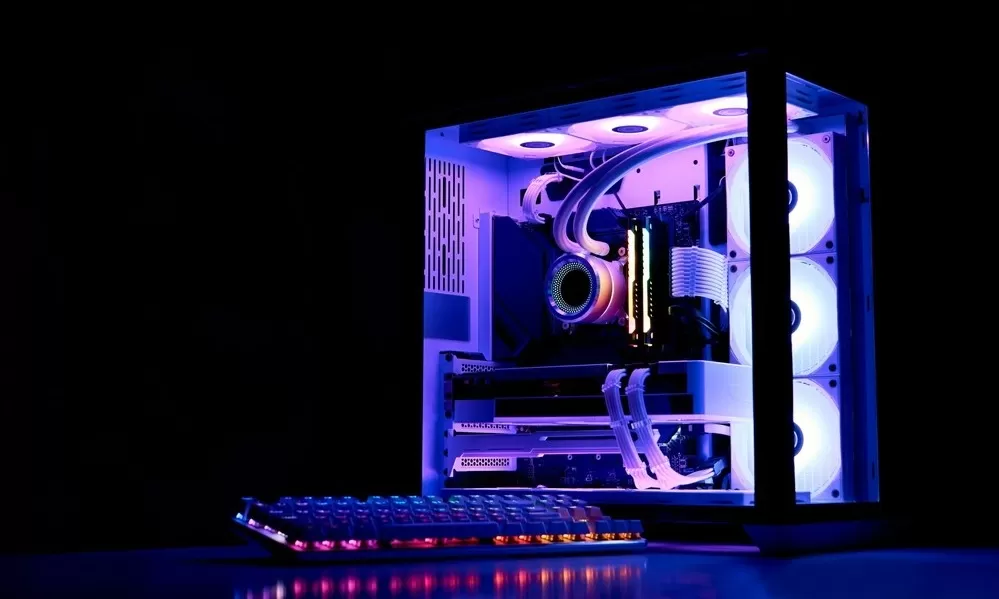
A liquid cooling system absorbs and dissipates heat from CPUs and GPUs using a coolant, usually water or a specialized liquid. Coolant circulates via water blocks linked to heat-generating components to transmit heat to a radiator, where fans remove it.
Air cooling uses heat sinks and fans. However, liquid cooling systems have better heat conductivity and can manage the thermal strain of high-performance computing workloads like overclocking. They also work silently owing to decreased fan speeds and provide aesthetic benefits with configurable settings. They are critical for personal computers and industrial applications where low operating temperatures guarantee system stability.
Basic Principles of Liquid Cooling
A liquid cooling system uses conduction and convection. The heat is first conducted from the component's IHS to the water block baseplate. Thermal paste conductivity lowers resistance. Since water conducts heat 30 times quicker than air, the water block coolant absorbs this heat. Convection transfers heat to radiator fins while coolant flows. The copper or aluminum radiator improves airflow surface area to dissipate heat into the surrounding air.
The coolant absorbs water block heat to start the liquid cooling cycle. Heated coolant is sent via tubing to the radiator, where it circulates through small channels with thin metal fins. The fins, cooled by fans, dissipate heat quickly. After cooling, the liquid returns to the water block to absorb additional heat. A continuous closed-loop procedure keeps ideal temperatures for high-performance components. Remember, a liquid cooling system may lower CPU temperatures more than air cooling for high-clock speed or overclocked computers.
Components of a Liquid Cooling System
Coolant Solution
Heat transfer efficiency depends on the liquid cooling system. For instance, distilled water is the most frequent form due to its high specific heat capacity (4.186 J/g°C) and thermal conductivity (0.624 W/mK). Cold-weather glycol mixes reduce freezing points and corrosion. Specialty coolants are pre-mixed with antimicrobial and thermal stability additives. Coolant selection influences system performance. However, coolant pH and conductivity must be regulated to preclude galvanic corrosion, particularly with mixed metals.
Pump
Liquid cooling systems circulate coolant around the loop via the pump. Most centrifugal pumps have high flow rates and head pressure. Diaphragm pumps, albeit rarer, regulate flow precisely and resist coolant particulates. When choosing a pump, match the flow rate to the system's resistance for constant flow under different situations. Reliability matters; pumps might be rated for tens of thousands of hours of continuous operation.
Radiator
A radiator dissipates coolant heat into the surroundings. Radiators may have different sizes in millimeters, like 120mm, 240mm, or 360mm, corresponding to single, dual, or triple-fan setups. Radiators with higher surface area and fans dissipate heat better. When choosing a radiator material, copper has superior thermal conductivity (398 W/mK) than aluminum (237 W/mK). Yet, aluminum is lighter and cheaper. Fin density in FPI (fins per inch) affects performance. Higher FPI increases surface area but may require higher static pressure fans.
Water Block
The water block immediately transfers heat to the coolant. High-performance water blocks optimize surface area contact using microfin or microchannel designs for heat transmission. Because of its thermal conductivity, CPU and GPU blocks might be copper but nickel-plated to avoid oxidation. Acrylic tops look good but impair thermal performance slightly. System flexibility decides whether to use a universal or component-specific water block. Meanwhile, component-specific blocks perform better thermally owing to tighter heat source contact.
Tubes and Fittings
A liquid cooling system's tubes and fittings carry coolant through the loop. PVC, rubber, and flexible silicone tubes vary in flexibility and kink resistance. Silicone is utilized in complex loops for its flexibility and high-temperature resistance. Tubes are attached to components by compression or barbed fittings. Compression fittings seal better and leak less, while quick disconnects are easier to maintain but limit additional flow. Tubing must be durable and chemically resistant in glycol or other specialist coolant systems to avoid deterioration.
Applications of Liquid Cooling
-
High-Performance Computing (HPC): In HPC environments, liquid cooling manages the immense heat from dense clusters of processors. It transfers heat away from CPUs and GPUs for temperature stability in supercomputers. Furthermore, liquid cooling facilitates higher rack densities for more computational power within limited space. It is key to progressive simulations and data processing tasks.
-
Gaming PCs and Workstations: Liquid cooling boosts thermal performance for gaming PCs and workstations because CPUs and GPUs can keep peak clock speeds during intense workloads. It benefits systems with overclocked components, where traditional air cooling would struggle. Also, with lower thermal throttling, liquid cooling gives consistent frame rates and processing power for rendering and gaming.
-
Industrial Applications: In industrial settings, liquid cooling helps regulate the heat from high-power electronics and machinery. It suits automation systems and power electronics. Moreover, liquid cooling extends the life of industrial components while preventing overheating and cutting maintenance time and costs in critical operations.
Future Trends in Liquid Cooling
Current data centers face rising power densities and heat production, so liquid cooling systems are getting better. Traditional air cooling cannot cool today's high-performance servers and AI accelerators, which may approach 50 kW per rack. Hotspots and lower efficiency result. Consequently, liquid cooling is 50-1000 times more efficient because it tackles thermal loads by circulating coolant in contact with heat-generating components.
It matters as data centers fulfill environmental targets. Liquid cooling decreases cooling energy usage by 10-20% for sustainability. The technology's capacity to utilize waste heat—up to 100 kW from a 42U rack—supports net-zero emissions. The small liquid cooling structure maximizes rack density. It allows modular, scalable installations that enable future development without retrofits to fix urbanization-related space restrictions. Hybrid cooling methods combine liquid and air systems and may save operating costs in legacy data centers.
Click here to discover T-Global industry-specific thermal management solutions.