In accordance with the European Union’s General Data Protection Regulation (GDPR), we are committed to safeguarding and ensuring your control over your personal data. By clicking “Accept All” you are permitting us to use cookies to enhance your browsing experience, assist us in analyzing website performance and usage, and deliver relevant marketing content. You can manage your cookie settings below. By clicking “Confirm” you are agreeing to the current settings.
Heat Pipe Design for Efficient Thermal Management
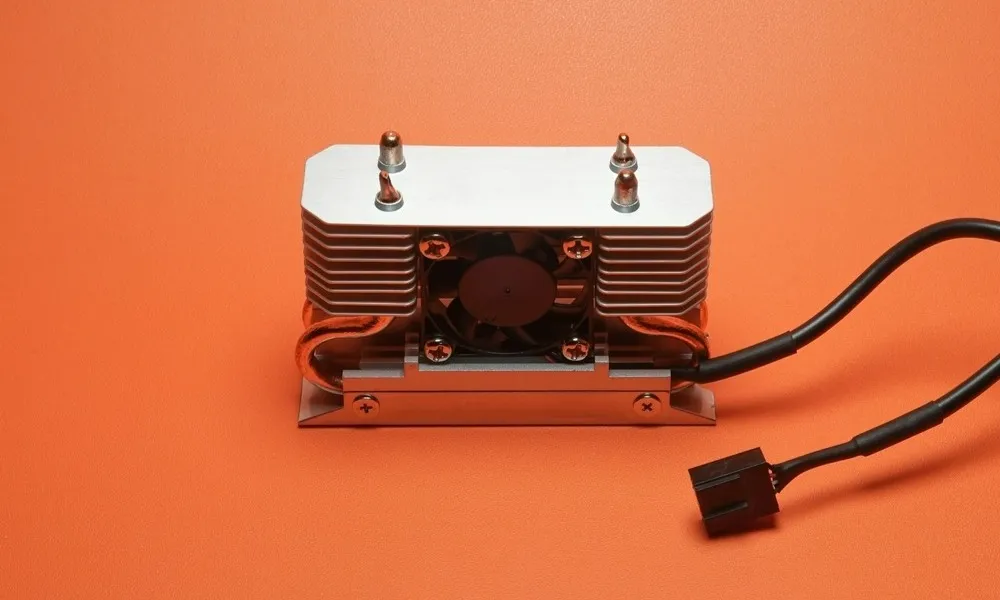
Heat pipes carry heat with little temperature difference and good thermal conductivity in thermal management, especially electronics. They optimize temperature management in minuscule, high-power electronics like laptops, servers, and spaceships via phase change and capillary action. Shape, wick structure, and material compatibility innovations in heat pipe design affect performance. Thus, specialized design boosts heat pipes' thermal load management while meeting rising cooling needs in technology-intensive workplaces.
Understanding Heat Pipes
Thermal management systems like heat pipes effectively transport heat. They use working fluids' high thermal conductivity and phase transition features for better heat transmission. Also, they carry heat over distances with minimum temperature loss because of their metallic exterior and interior-wicking structure. Along these lines, heat pipe design is essential in advanced thermal management systems, especially when conduction techniques fail.
• Heat Transfer Mechanism in Heat Pipes
Heat pipes use phase change, conduction, and convection to convey heat. The heat pipe's working fluid absorbs heat and turns liquid to vapor at the evaporator. The cooler condenser part releases heat and condenses this vapor into a liquid. The heat pipe's wick construction allows liquid to return to the evaporator via capillary action, completing the cycle. Hence, heat pipes transmit heat with low thermal resistance, which is helpful against gravity forces.
• Importance of Heat Pipes in Various Industries
Heat pipes are key in electronics cooling and other sectors. They help cool electronic components, including CPUs in computers, servers, medical devices, and spacecraft. Manufacturers may regulate thermal loads and protect sensitive components with heat pipes in system design. For instance, laptop cooling uses heat pipes to remove heat from the CPU without impacting performance. Plus, with their high power densities and compactness pushing the limits of thermal engineering, modern electronics need good heat management.
Key Design Considerations for Heat Pipes
Material, size, and shape are vital to performance in heat pipe design.
Material affects heat pipe thermal conductivity and working fluid compatibility for heat transmission. For example, copper is used for electronic cooling thanks to its strong thermal conductivity and compatibility with water. Application-specific thermal and spatial constraints determine heat pipe size and shape. Compact electronic gadgets use flat heat pipes, or vapor chambers, owing to their space efficiency and heat dispersion.
Heat pipe design counts on the wick structure for capillary action and efficient fluid transfer. For situations where gravity is less critical, sintered copper powder has noteworthy capillary action. The operating temperature limits of sintered copper water heat pipes are 0-250°C. Meanwhile, water is employed as a working fluid because of its thermal characteristics within a typical electronics operating temperature range. An example of water content in heat pipes is that a 6mm, 150mm length pipe contains about 1cc of water. Still, capillary, sonic, boiling, and entrainment restrictions limit heat pipes' thermal conductivity and transmission rates.
• Material Selection
Copper and aluminum heat pipe materials differ in thermal conductivity and efficiency. As mentioned, in high-performing heat pipe designs, pipes are made of copper due to its thermal conductivity. Because of its heat transfer and working fluid compatibility, copper heat pipes may be used in anything from personal computer devices to aircraft technology. Aluminum has lesser heat conductivity than copper but is lighter and cheaper. Aluminum heat pipes are better for situations where weight and cost matter more than heat transmission efficiency.
Remember, heat pipe design material impacts heat conductivity, lifespan, and corrosion resistance, which are fundamental in applications with high-reliability requirements. For your information, the typical lifespan of heat pipes should be at least 20 years.
• Sizing and Shape
Designers must balance thermal and physical restrictions when choosing heat pipe sizes and shapes for particular applications. Thin, flat heat pipes are needed in tiny electronics like laptops to disperse heat. Round heat pipes with larger diameters may be used in server cooling solutions to increase heat transmission and power dissipation. In heat pipe design, length impacts thermal resistance and heat transfer efficiency. Heat pipe thermal resistance calculation: is done while dividing Delta-T divided the power input. Longer heat pipes may carry heat further but have higher thermal resistance and lower heat transmission.
So, to optimize the heat pipe's shape and dimensions for the use case, the application's thermal needs, available space, and required heat transfer efficiency are carefully evaluated.
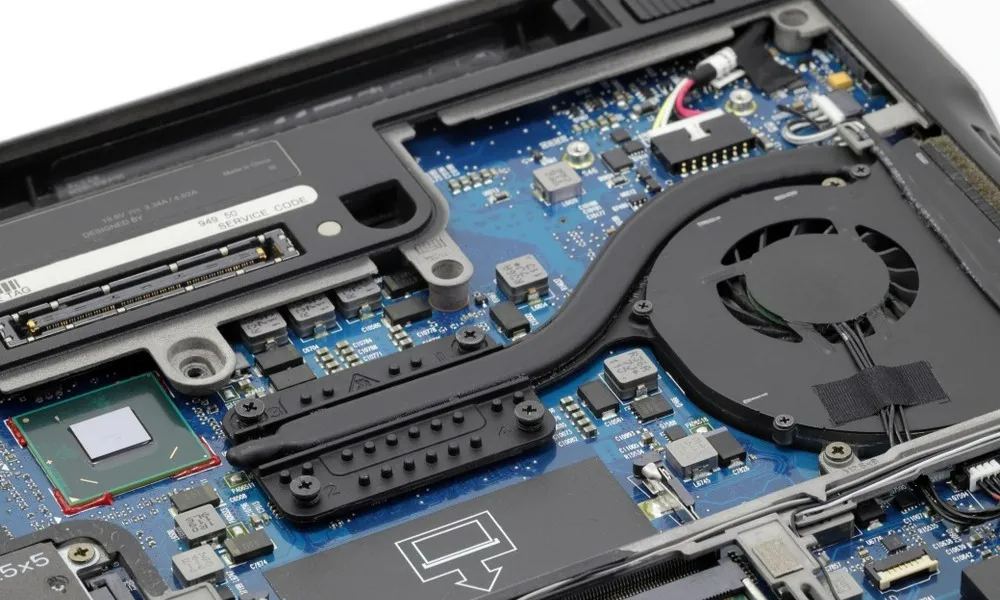
Advanced Heat Pipe Design Techniques
Innovative heat pipe designs maximize thermal conductivity and efficiency. Ultra-fine fibers or bi-porous sintered materials in wick architectures improve capillary action for faster and more efficient heat transmission in various orientations. Adding phase-change materials to the heat pipe design promotes thermal responsiveness under varying thermal loads for augmented performance. These heat pipe design changes allow larger heat fluxes and more geometric flexibility for small and irregularly shaped electronic devices.
Custom Solutions for Challenging Thermal Management Scenarios
Advanced electronics and aerospace applications need custom heat pipe designs to solve thermal management issues. Heating pipes with varying cross-sections or flexible couplings may fit complicated assembly space restrictions. Besides, the heat pipe's performance is optimized by employing ammonia for low-temperature activities or sodium for high-temperature operations. Heat pipes with robust materials and reinforced constructions last longer in adverse conditions like space applications. Subsequently, customized heat pipe designs control heat dispersion in the most demanding thermal management situations.
Navigating Challenges in Heat Pipe Design
Dispelling heat pipe operating restrictions and material compatibility myths is prevalent in heat pipe design. The assumption that thermal conductivity is constant regardless of length or orientation is a common heat pipe design mistake. Actually, the heat pipe's length, gravity direction, and wick construction (sintered powder or axial groove) affect its thermal conductivity and capillary action. Furthermore, the working fluid and pipe material must be compatible to avoid chemical reactions like oxidation from impairing heat pipe operation.
How to Optimize Heat Pipe Performance in Complex Systems?
Heat pipe integration with other system components maximizes complex system performance. Matching the evaporator and condenser to the heat source and sink is necessary in heat pipe design. Custom curving or bending of heat pipes may be required. The typical bend radius for heat pipes can exceed 3 times the heat pipe's outer diameter. Yet, these modifications might reduce heat transmission capacity if accomplished carelessly. For example, every 45-degree bend can decrease Qmax by approximately 2.5%.
Simulating heat pipe performance under varied operating situations using computational fluid dynamics (CFD) modeling is helpful. What is more, flat heat pipes or vapor chambers may transfer heat without the bulk of round pipes in systems with limited space. Moving the theoretical design to real-world use requires comprehensive testing under realistic circumstances to verify the heat pipe satisfies performance parameters.
Thermal management in high-tech devices requires careful heat pipe design for performance and dependability. At T-Global, we leverage our thermal engineering skills for unique heat pipe solutions. Our industry-specific technologies provide effective heat management in numerous applications. Contact us for accurate and customizable heat pipe design solutions.