In accordance with the European Union’s General Data Protection Regulation (GDPR), we are committed to safeguarding and ensuring your control over your personal data. By clicking “Accept All” you are permitting us to use cookies to enhance your browsing experience, assist us in analyzing website performance and usage, and deliver relevant marketing content. You can manage your cookie settings below. By clicking “Confirm” you are agreeing to the current settings.
Instruction on Calculating Heat Sink Size
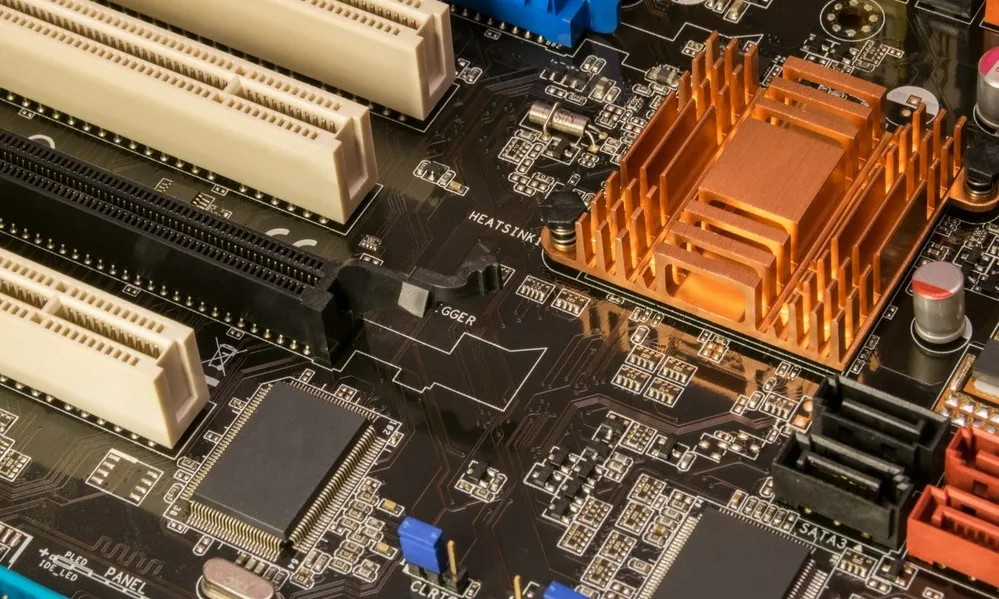
Heat sink size matters in electronics cooling, affecting device efficiency and life. Calculating heat sink size requires an understanding of thermal dynamics and material characteristics. While integrating thermal design power, ambient temperature restrictions, and material thermal conductivity, a heat sink size calculator simplifies this problematic procedure.
When determining heat sink size, the calculator simplifies volumetric thermal resistance and ideal fin dimensions for efficient heat dissipation. Fin type, number, and material also affect heatsink calculation. The calculator correctly calculates fin height, thickness, and heat sink size to keep the device cool and maximize performance. So, these tools improve design accuracy and decrease the time and complexity of cooling solution creation.
Key Input Parameters for the Calculator
-
Heat Source Power (Q)
-
Tcase Max
-
Max Ambient Temperature
-
Thermal Budget
-
Volumetric Thermal Resistance (Rv)
-
Airflow (LFM or m/s)
-
Altitude (for Rv derating)
-
Heat Sink Dimensions (Length, Width, Height)
-
Fin Type, Material, Number, Thickness, and Height
Significance of Parameters in Heat Sink Sizing
These features aid in calculating heat sink size. First, Heat Source Power (Q) and Tcase Max affect the heat sink's thermal load. Meanwhile, the Max Ambient Temperature and Thermal Budget determine environmental limits and the maximum temperature rise. The heat sink's heat dissipation efficiency per unit volume depends on Volumetric Thermal Resistance (Rv).
Airflow rates can affect cooling performance in natural convection. Rv must be adjusted for altitude applications to accommodate air density differences. Finally, heat sink size and fin parameters impact heat transfer surface area. These inputs guarantee accurate heatsink calculations that meet the device's thermal management demands for optimized efficiency.
Navigating the Calculator Interface
-
Select 'Heat Source Power (Q)': Input your chip's maximum heat in watts.
-
Enter 'Tcase Max': Type in the maximum temperature of the chip case.
-
Specify 'Max Ambient': Record the highest ambient temperature for operation.
-
Calculate 'Thermal Budget': Deduct 'Max Ambient' from 'Tcase Max.'
-
Choose 'Volumetric Thermal Resistance (Rv)': Pick an Rv value based on airflow.
-
Adjust for Altitude: Modify the Rv value if the device operates at high altitudes.
-
Determine Heat Sink Dimensions: Input proposed length, width, and height.
Tips for Accurately Filling out Each Field
In calculating heat sink size, correct data and measurements are required. Valid 'Heat Source Power (Q)' from the chip manufacturer, the chip's 'Tcase Max' threshold temperature, and the extreme environment's 'Max Ambient' temperature are key for an ideal heatsink calculation.
The 'Thermal Budget' determines the heat sink's efficiency, while the 'Volumetric Thermal Resistance (Rv)' balances overheating and oversizing. Altitude adjustments are also vital. Advanced tips involve balancing efficient cooling with space and material limits, including chip airflow, thermal gradients, and conservative estimations for variable ambient conditions.
Advanced Considerations in Heat Sink Size Calculation
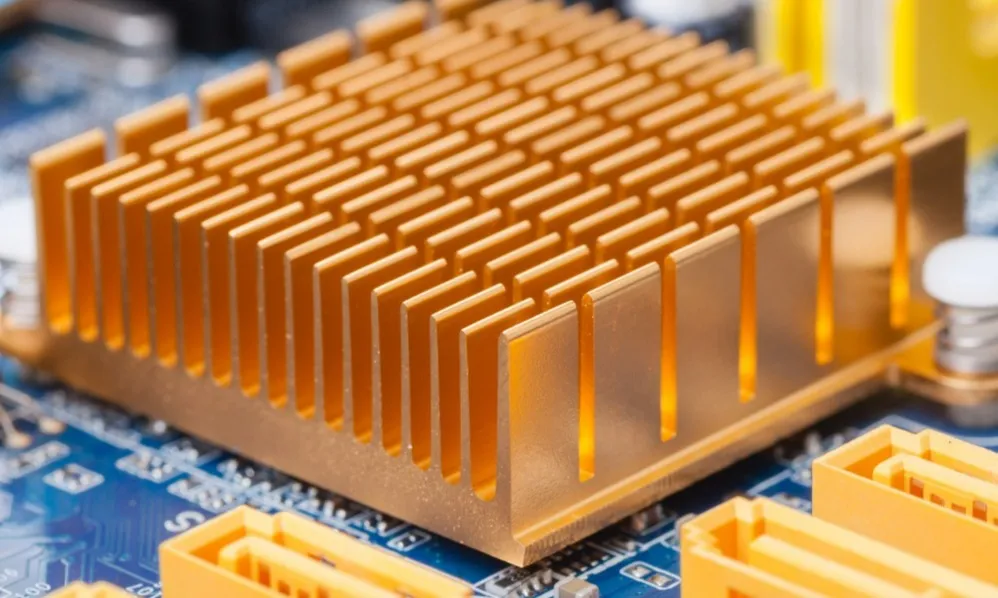
Calculating heat sink size calls for knowing Volumetric Thermal Resistance (Rv). It measures the heat sink's heat dissipation per unit volume, considering its dimensions and material qualities. The formula for calculating Rv is ΔT/Q, where ΔT is the temperature differential between the heat source and ambient environment, and Q is the heat power dissipated.
Heat sink efficiency and size depend on this resistance, which controls thermal load management. In practical scenarios, Rv helps estimate the heat sink volume for a given heat load since greater Rv values imply worse thermal dissipation efficiency.
How to Adjust Rv based on Airflow and Heat Sink Volume?
Adjusting Rv for airflow and heat sink volume is vital in heatsink calculation. Airflow affects heat sink thermal performance by lowering Rv for a smaller heat sink volume for the same heat dissipation. E.g., a suitable Rv value is critical in a moderate airflow condition (2.5 m/s).
For heat sink volumes under 300 cm³, a lower Rv value accounts for greater airflow and efficiency. A higher Rv value is necessary for heat sinks beyond 1000 cm³ due to reduced airflow efficiency per unit volume. Optimizing heat sink designs for individual applications requires this modification for effective thermal management within spatial limits.
Dealing with Special Scenarios
Modifying Calculations for High Altitudes
Calculating heat sink size for devices operating at high altitudes must account for lower air density, which decreases heat dissipation efficiency. Thinner air at higher altitudes lowers the convective heat transfer coefficient. The heatsink calculation volumetric thermal resistance (Rv) values must be adjusted. It should be derated by 10% each mile of altitude.
Insights into Two-Phase Cooling for Low Thermal Budgets
Two-phase cooling works well when the thermal budget is below 40 degrees Celsius. This cooling technology uses latent heat of vaporization in heat pipes or vapor chambers. In such settings, calculating heat sink size must account for coolant phase change heat transfer.
These systems can manage larger heat fluxes with a lower heat source-sink temperature differential than air-cooled heat sinks. It helps small electronic devices with high heat dissipation but limited space. The two-phase system's effective thermal conductivity may be much greater than solid metals. Hence, the heat sink design must compensate for that.
Interpreting Calculator Results
It would help if you grasped the link between volume and thermal performance to interpret heat sink calculator findings, mainly when calculating heat sink size. The volume is determined by heat source power (Q), thermal resistance (Rv), and thermal budget (ΔT).
You must convert this volume into proportions matching your device's space. A bigger volume requires more heat dissipation, which may be increased by fin height, width, or length. But remember that taller fins promote convection, and wider fins boost radiation.
How to Modify Heat Sink Dimensions within Spatial Constraints?
When altering heat sink size within spatial limits, heatsink calculation results must meet physical space. If vertical orientation and natural convection are used, you could increase fin height rather than base area if the calculated volume predicts a greater heat sink than space.
Alternatively, increasing fin density might compensate for a decreased fin height or base area. It must be done carefully since excessive fin density might limit airflow and convection efficiency. Fin thickness and spacing must be adjusted with the fixed length and width. Thinner fins enhance surface area but need a high-conductivity material for heat transfer.
Conclusion
Electronic device thermal management requires calculating heat sink size accurately. A proper heatsink calculation considers heat source power, maximum case temperature, and ambient temperature, among others. Meanwhile, a heat sink size calculator simplifies this process while determining ideal dimensions and materials for heat dispersion.
As part of our heat sink solutions, We offer metal heat sinks from small aluminum units for circuit boards to bigger, custom-shaped ones. We offer conventional and bespoke heat sinks with novel fastening mechanisms for simple installation. With experience in thermal management technology, we develop heat sinks for air or liquid cooling. T-Global adheres to standards and certifications for quality thermal engineering solutions.